Keynote Speakers
The organising committee is pleased to confirm the following Keynote Speakers for MSC2015.
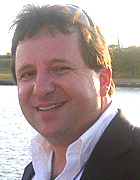
Danny Abramovitch
Agilent Labs
Danny Abramovitch earned degrees in Electrical Engineering from Clemson (BS) and Stanford (MS and Ph.D.), doing his doctoral work under the direction of Gene Franklin. Upon graduation, and after a brief stay at Ford Aerospace, he accepted a job at Hewlett-Packard Labs, working on control issues for optical and magnetic disk drives for 11 1/2 years. He moved to Agilent Laboratories shortly after the spin off from Hewlett-Packard, where he has spent the last 14 years working on test and measurement systems.
Danny is a Senior Member of the IEEE and was Vice Chair for Industry and Applications for the 2004 American Control Conference (ACC) in Boston. He was Vice Chair for Workshops at the 2006 ACC in Minneapolis, for Special Sessions at the 2007 ACC in New York, and for Industry and Applications for the 2009 ACC in St. Louis. He was Program Chair for the 2013 ACC and is General Chair of the upcoming 2016 ACC. He has helped organize conference tutorial sessions on topics as varied as disk drives, atomic force microscopes, phase-locked loops, laser interferometry, and how business models and mechanics affect control design. He served as the Chair of the IEEE CSS History Committee from 2001 to 2010. Danny is credited with the original idea for the clocking mechanism behind the DVD+RW optical disk format and is co-inventor on the fundamental patent. He was on the team that prototyped Agilent's first 40Gbps Bit Error Rate Tester (BERT) and was able to cite a Douglas Adams book in one of his patents relating to that device. Along with his co-author, Gene Franklin, he was awarded the 2003 IEEE Control Systems Magazine Outstanding Paper Award. His favorite paper remains the one prompted by a question from his then 3-year-old son, which showed that the outrigger was a feedback mechanism that predated the water clock by at least a 1000 years. His recent work for Agilent was on future atomic force microscopes and high precision interferometers. He is currently looking at improving the real time signal processing on Agilent's Mass Spectrometers. He is the holder of over 20 patents and has published over 40 reviewed technical papers.
View AbstractTrying to Keep it Real: 25 Years of Trying to Get the Stuff I Learned in Grad School to Work on Mechatronic Systems
This paper is about the difficulty of making academic control techniques work in an industrial environment, particularly with mechatronic systems that have large numbers of flexible modes. I will go through the methods that fail if done the standard way and the adjustments I have learned to make over the years which gets a lot of them to work. I will also go over the methods that seem to work robustly and without much thought in the industrial environment, explaining why they do work. Finally, I will try to show that understanding the differences and commonalities in these two world views allows us to use the principles of one to improve the other.
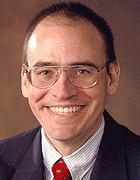
Richard D. Braatz
Massachusetts Institute of Technology (MIT)
Richard D. Braatz is the Edwin R. Gilliland Professor at the Massachusetts Institute of Technology (MIT) where he does research in control theory and its application. He received M.S. and Ph.D. degrees from the California Institute of Technology and was formerly on the faculty at the University of Illinois at Urbana-Champaign and a Visiting Scholar at Harvard University. He has consulted or collaborated with more than 20 companies. Honors include the AACC Donald P. Eckman Award, the Antonio Ruberti Young Researcher Prize, and the IEEE Control Systems Society Transition to Practice Award. He is a Fellow of IEEE and IFAC.
View AbstractControl Systems Technology in the Advanced Manufacturing of Biologic Drugs
This presentation describes the systems integration and control design for a platform for manufacturing biologic drug compounds from start to ready-to-use biologic drug in less than 40 hours (current manufacturing takes about 6 months). The overall team for this ~$10M DARPA project is designing new yeast strains, designing small-scale process equipment, developing real-time sensors, and employing feedback controls. Although the manufacturing process uses biological cells, the talk does not require any background in biology, and is focused on the design of the manufacturing platform from scratch, including process scheduling, mixed continuous-discrete modeling, nonlinear feedback control, and plantwide control.
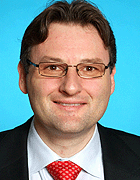
Andreas Kugi
Vienna University of Technology, Austria
Andreas Kugi is head of the Automation and Control Institute (ACIN) and full professor for Complex Dynamical Systems at Vienna University of Technology in Austria. He received the Dipl.-Ing. degree in Electrical Engineering in 1992 from Graz University of Technology, Austria, the Ph.D. (Dr.techn.) and the ”Habilitation” degree in the field of automatic control and control theory from Johannes Kepler University (JKU), Linz, Austria, in 1995 and 2000, respectively. His research interests include the physics-based modeling and control of (nonlinear) mechatronic systems, differential geometric and algebraic methods for nonlinear control, and control design for infinite-dimensional systems. He is involved in industrial research projects with more than 40 companies. These projects cover the fields of automotive applications, hydraulic, pneumatic, and electrical drives, smart structures, and rolling mill applications. He has published about 200 scientific publications, holds about 30 patents, and is the Editor-in Chief of Control Engineering Practice. Since 2010, he is a corresponding member of the Austrian Academy of Sciences.
View AbstractModel-based Process Control in the Steel Industry
The steel industry is confronted with an increased competition demanding for more diversified product portfolios, tighter quality tolerances, increased energy efficiency, as well as reduced waste and environmental impact under volatile energy and raw material prices. Advanced process control and automation are important value drivers to improve the production capabilities, the sustainability, the flexibility, and the efficiency of the various production processes. These processes feature many challenging properties for a control engineer: nonlinearities, MIMO coupling, different time scales, transport delay, strong parameter variations, scarcity of measurments, rough environmental conditions. Thus, model-based analysis and control design concepts turn out to play a key role. In this talk, we will give some selected industrial applications from steel industry with a special focus on the interplay between the control theoretic background and the practical implementation.
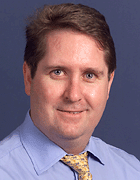
Ross McAree
University of Queensland
Ross McAree is the Joy Global Professor of Mechanical Engineering at the University of Queensland. His research interests are in safety critical control systems, constrained predictive control, state and parameter estimation, and realtime control systems. He leads the Smart Machines Group in the School of Mechanical and Mining Engineering group comprising 2 academic staff, 5 Postdoctoral Research Fellows, 9 research engineers, and 5 PhD students. He received his PhD from the University of Melbourne and from 1993 to 1999 was a postdoctoral research fellow in the Robotics Research Group at Oxford University and a Lecturer in Engineering at Trinity College, Oxford. He joined The University of Queensland in 1999, where he has served as Program Director for Mechatronic Engineering (2002-2005 and 2007-2011, 2013-continuing), Chair of the School of Engineering Teaching and Learning Committee (2007) and Chair of the School of Mechanical and Mining Engineering Research Committee (2009- continuing). In 2013 he was elected a Fellow of the Australian Academy of Technological Sciences and Engineering in recognition of the impact of his work in Automation for the mining industry.
View Abstract